Maximus 7.2 - Physics based Multiphase Flow Simulator
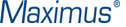
Released: June 2021, Service Pack - April 2022
Maintained until July 2024
About Maximus
Maximus is a very powerful and versatile compositional and black oil production and flow assurance modelling software, capable of simulating the whole production and transport facilities network, from the reservoir to the early stages of separation, throughout the life of the field. Through the native integration of Multiflash and its field planning modelling capabilities, production and flow assurance engineers and project managers can easily model in details the entire asset and access relevant information for their discipline to optimize decision making and minimize the risks associated with production such as formation of solids (hydrates, waxes, asphaltenes, scales etc.), corrosion/erosion of the facilities and other potential obstacles to the correct operations and optimal field development. Engineers can also easily assess options, perform “what if” analyses and compare operating scenarios and design choices, in order to make the best choice, based on the business objectives previously set, and within the real constraints of the asset.
What's new in Maximus 7.2
After the release of v7.1 which saw a major effort in tigtheing the connection between Maximus and Multiflash and extending the GUI functionalities to enhance the accessibility of advanced features of Maximus, version 7.2 comes with significant improvements and new functionalities.
Among various enhancements, we have introduced the possibility of elevation and geo-location of pipelines' profiles segments directly from a GIS map, thorugh the integration of ESRI ArcGIS. This will allow engineers to design networks more easily with the required level of details, accessing the accurate altimetry and bathimetry data from the ESRI geodatabase.
To renew and give a more modern and fresher look to the GUI, we have added a brand new, cleaner and simple ribbon bar, as an alternative to the standard toolbar and menubar interface.
The integration with Multiflash has been tigtened even further, to allow users to make of the Multiflash workflows and general fluid configuration as the default way of definining fluids and physical properties models in Maximus.
Further enhancements include the development of a new tank object unit operation to simulate the storage of liquid as source or accumulation, the extensions of the cooldown time calculator to integrate with flow assurance predictions, and several improvements in FloWax, to allow the simulation of the effect of wax removal from a pig run, and sensitivity studies with wax parameters.
From the architectural point of view, a great effort has been dedicated to the development of the cloud version of Maximus, with the introduction of a new Restful API allowing to interface with the Maximus engine to specify models and run simulations in the cloud.
List of changes in Maximus 7.2
- New functionalities
- Added an ArcGIS Map View from Esri, allowing models to be designed on a world map and for longitude, latitude and elevation data to be read from Esri REST services
- Included with the ArcGIS Map View is the ability to load shape files and convert into pipeline profiles
- Added a new Storage Tank object
- Added the ability to modify the variables being shown on the flyby tooltips of objects, as well as increased the number of variables available
- User experience
- Added a ribbon bar interface, which can be switched to by going to the General Setup dialog, GUI Settings tab*
- Added the ability to merge multiple pipelines together into one pipeline by selecting the pipelines on the canvas, right clicking and selecting the "Merge Selected Pipelines" option
- Cool Down time estimator has been improved to include options to run to a fixed time or to the wax/hydrate forming temperature
- Cool Down time estimator is now accessible via Open Interface and the Excel Add-In
- Cool Down time estimator performance improvements have been made when using the discretisation option
- Added LedaPM 2.6.260.019 steady state plug-in module
- Improvement made to the Hydraulic Potential Controller event logic creation to include information provided by the Well Stabiliser object (if set up)
- Added a Well Abandonment wizard that utilises the Well Stabiliser object to optimally turn off a well depending on its minimum stable flowrate
- Control Choke Compressor has been improved to include all the functionality of the compressor while also keeping its original functionality of specifying multiple constraints
- PVT extensions
- Improved the workflow between Multiflash and Maximus, with changes to how compositions are created and modified
- FloWax improvements
- Added the ability to pig and continue a simulation and to get wax accumulation data from a previous wax case
- You can now run FloWax Sensitivity Studies, including via Open Interface and the Excel Add-In, to modfy in steps wax parameters such as porosity and mass transfer multiplier.
- Architectural
- Added RestAPI to run Maximus in the cloud
- Extended command line interface to support a Python interface
- Various performance improvements and enhanced parallelisation